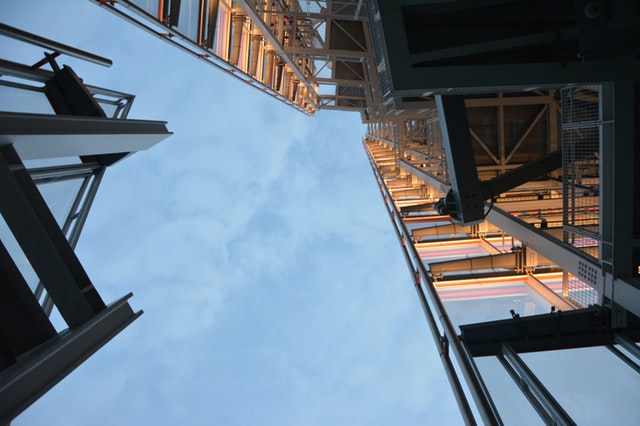
Working at height is one of the biggest causes for workplace fatalities and serious injuries which are often because of a fall from a ladder or falling through a fragile roof. A fall from height is defined as a fall from one level to another. With careful planning and management working at height can be conducted safely.
Working at height can be found in all industries, you may think you do not conduct any working at height activities but think about what happens if the light bulb needed to be replaced, as often or not this activity is undertaken by the use of a step ladder. Although the frequency of working at height may differ depending on the industry the risk will remain however that risk will still need to be managed.
Fall from Height | The Risks
As an employer you have a legal duty to ensure the safety, health and welfare of your employees as so far as is reasonably practicable and the law governing working at height, the Work at Height Regulations 2005, places a duty on the employer or those in control of any work at height activity to prevent the risk of death or injury caused by a fall from height. Although there is a legal duty placed upon the employer or those in control of any work at height, the employee also has a legal duty to take reasonable care of themselves and others who may be affected by their actions as well as cooperating with their employer so that they can fully discharge their duties under Section 2 of the Health and Safety at Work etc. Act 1974.
To begin with, every employer legally is required to conduct a suitable and sufficient risk assessment for working at height under regulation 3 of The Management of Health and Safety at Work Regulations 1999. As part of this risk assessment, you need to look at the hierarchy of controls. Firstly, can working at height be eliminated? Can the work at height be undertaken at ground level? Nowadays, we often see window cleaners using extendable poles rather than working from a ladder, therefore, they have removed the need to work at height. Think about how much of the work can be completed at ground level rather than having to do it at height. Where possible, work at height should be designed out wherever practicable.
If working at height cannot be eliminated, the next step is to prevent a fall from occurring. The main places where falls occur include in incidence order from the HSE:
- Ladders: 40%
- Vehicles/FLTs: 17%
- Machinery/plant: 10%
- Platforms:10%
- Stairs: 8%
- Roof/false ceiling: 7%
- Scaffold/gantry: 4%
- Warehouse racking: 4%
One of the main reasons why a fall has occurred is because of the incorrect type of access equipment has been used.
In addition, falls on stairs account for a third of all reported accidents due to the stairs being contaminated for example, liquid spills, food product(s) or employees wearing inappropriate footwear.
Putting Preventative Measures in Place
Where there is a risk of a fall, preventative measures must be taken to minimise the likelihood of a fall from height. Think about the type of access equipment to prevent people from falling to illustrate this, mobile elevating work platform (MEWP), the intention of the MEWP is to have persons access it from ground level which is extended up to allow that person to work safely at height they are generally not used for transferring persons from one level to another. However, it is essential prior to selecting a MEWP that the correct type of MEWP is selected and that the work has been thoroughly planned and to think about where the access equipment is to be placed.
For some work, the existing roof structure, vehicle roof, mezzanine, may already be adapted by having a fixed guard installed, so these areas should be used. If a working at height preventative measure has already been installed this should be considered first. In order to restrain travel, employees could wear personal protection in the form of a work restraint which prevents the individual getting into a fall position.
If you cannot prevent a fall occurring, then you need to think about minimising the distance and/or a consequence of a fall. Often used in construction sites, soft landing systems are used such as air bags, which will help reduce the consequence of the fall.
By having in place a fall-arrest system such as a harness and lanyard and by using a high anchor point can also reduce the distance and consequences of a fall.
Fall from Height & Ladder Safety
If the task is considered to be low-risk and of short duration, a sensible and practicable option could be the use of ladders and stepladders. Ladders and stepladders are not banned in the workplace and can be the most suitable piece of work equipment to work at height. Going back to the introduction of this article, changing a lightbulb in an office, will mostly consist of the use of a step ladder. Even a simple task like this, always ensure that the right type of ladder is used for the job, that the person using the ladder is competent, the equipment is maintained in a good safe condition and subject to inspections. For more information regarding ladders, please see our article on Ladder Safety- New Code of Practice.
Most accidents that have resulted in a fall from height could have easily been prevented. Whenever someone is required to work at height to carry out a task a thorough risk assessment must be carried out, a safe system of work implemented and the work thoroughly planned, also taking into consideration other persons as to not put them at risk. Never underestimate the risks involved. Simply advising employees to ‘take care’ when using access equipment or working at height is not enough; proper precautions must be taken.
Never just opt for the cheapest and quickest piece of access equipment as it may not be suitable, think about all the ways in which the person working at height could be at risk of falling and identify measures how to prevent this as so far as is reasonably practicable.
It is also important to think about other hazards and whether any controls implemented for reducing the likelihood of harm occurring from those other hazards would then increase a fall from working at height.
Any equipment required for working at height must be maintained in a good safe working condition. There must be no defects to any of the equipment that you use. Equipment should be regularly inspected and always inspected prior to use. It is important that any employee using access equipment knows how to do so safely, and that any necessary training or supervision is provided.
Tower Scaffold Safety
Where tower scaffolds are to be erected or dismantled, this task should only be carried out by those persons who have undertaken the relevant training such as PASMA. For more information on mobile tower scaffolds please our article on Mobile Scaffold Tower Safety - An Essential Guide for Employers.
Within The Work at Height Regulations, there are 19 regulations and eight schedules. The eight schedules are:
- Requirements for existing places of work and means of access or egress at height.
- Requirements for guard-rails, toe-boards, barriers and similar collective means of protection.
- Requirements for working platforms.
- Requirements for collective safeguards for arresting falls.
- Requirements for personal fall protection systems.
- Requirements For Ladders.
- Particulars to be included in a report of inspection.
- Revocation Of Instruments.
The regulations discuss the duties that employers should take to minimise the risk of a fall occurring, the regulations also discuss fragile surfaces and what an employer should do.
To conclude, working at height is a high-risk category and site-specific risk assessments must be carried out to minimise the likelihood of a fall occurring. Most accidents involving a fall from height can be easily prevented if the correct piece of equipment selected is appropriate for the task, that the equipment is maintained and that the person working at height is competent to do so.
For safety advice and support you can trust, get in touch with our team of Health and Safety Consultants today.