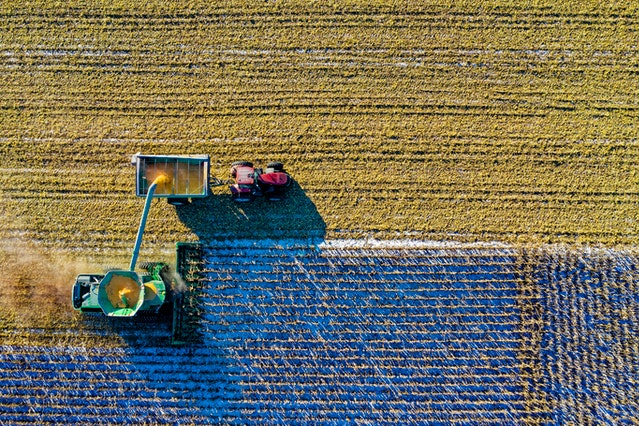
It has been said that British farming is some of the best in the world and who would argue? Agriculture’s importance to the UK economy is emphasised by the fact that the UK has an estimated 149,000 farm businesses. That's more than the number of businesses involved in the motor trade, education, finance and insurance. We review the issues surrounding health and safety on farms and provide practical guidance to help businesses with their safety compliance.
Health and Safety on Farms | Counting the Cost
It is also estimated the agricultural industry in general accounts for around one per cent of the workforce in Great Britain, yet it accounts for 20 per cent of worker deaths. Many of these deaths are due to poor working practices while carrying out maintenance on machinery. In addition, many more workers are seriously injured each year due to unsafe working practices while working on machinery.
What should a farm with good Health & Safety Management look like?
The Health and Safety Executive (HSE) have published a guidance document that sets out what a good farm should look like. So rather than begin with horrendous statistics involving serious and fatal accidents, let’s set a positive tone and have an overview of the key points within this guide which provides information on how these examples can be made safe.
Vehicles and Machinery
- Driver/operator behaviour.
- Telehandlers and lift trucks.
- All-Terrain Vehicles (ATV’s).
- Pedestrians.
- Maintenance.
Falls from Height and Falling Objects
- Access equipment.
- Work on fragile roofs.
- Bales and trailers.
Children
Overhead Power Lines (OHPLs)
Cattle
- Handling.
- Field with public access.
Drowning and Asphyxiation
Asbestos
Moving loads by hand
- Mechanisation.
- Risk reduction measures.
Animal Diseases
Noise
Pesticides
- Storage and transportation.
- Application.
Chainsaws
- Training.
- Location.
- Saws and protective clothing.
Electrical Systems
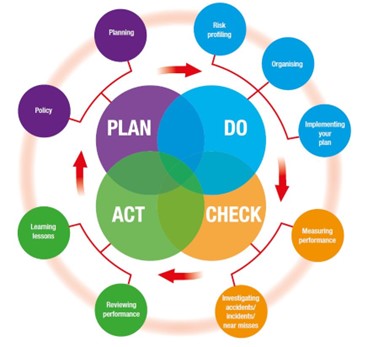
As with all sectors in the UK an effective H&S Management System lays the foundation for effective H&S Management and legal compliance. For example the model to the right based on the Health and Safety Executive’s defined guidelines as set out in the guidance note ‘HSG65’ utilises agreed principles to achieve ones intentions and goals: a safe place of work. It follows the Plan, Do, Check, Act, concept of risk management.
In my capacity as a H&S Consultant while visiting farms, what was apparent to me is that farmers and their workers, work extremely hard, they work long hours, they work unsocial hours and often in very inclement weather, so how can they find time to manage health and safety?
Unlike other management systems farmers have to deal with on a day-to-day basis, H&S is more forgiving in that it is an ongoing process and if the guidelines are applied H&S Management System goals will be achieved.
Help is at Hand
Regulation 7 (Health and safety assistance) of the Management of Health and Safety at Work Regulations requires that employers appoint one or more competent person (s) to assist in undertaking the measures one needs to take to comply with the requirements and prohibitions imposed by or under the relevant statutory provisions and by Part II of the Fire Precautions (Workplace) Regulations 1997.
Risk Assessment Process
A key fundamental and important element of a H&S Management System is the risk assessment process, get it right and all other elements of your Management System should fall into place.
Health and Safety on Farms | Essential Guidance
Carry out a task analysis, use the key points highlighted earlier from the guide ‘what a good farm looks like’ as a starting point to help you identify what needs to be risk assessed. For example:
- Make a list of all the different types of agricultural machinery and equipment you have and carry out suitable and sufficient risk assessments.
- Make a list of all routine activities that involve ‘work at height’ e.g. baling and working from trailers and non-routine tasks such as roof repairs.
- Consider the working environments you will be working in e.g. working near to overhead power lines, or operating machinery on hillsides or slopes.
- Livestock handling should be on your task list for risk assessment.
- Activities involving work in an around slurry pits and slurry tanks.
- Assess if there is asbestos on your premises, has an asbestos survey been undertaken, is there a management plan in place?
- Carry out a risk assessment on the potential of animal diseases especially when handling livestock.
- Your risk assessments should, where relevant, cover physical hazards that can lead to occupational health issues such noise and vibration (both hand/arm and whole body).
- Moving loads by hand i.e. manual handling operations.
- The assessment to health from exposure to hazardous substances including those generated by process e.g. dusts and may include pesticides and veterinary medicines.
- Assess the risks associated with fixed electrical installations and equipment.
- Decide what control measures are needed and develop a plan to ensure they are implemented.
Provide employees and others with:
- Information about the hazards and risks that have been identified.
- Instruction and training on the control measures and procedures; and
- How to report any problems with the control measure/procedures and any defects to equipment, guarding and other safety devices.
Monitor your activities to ensure control measures and procedures are effective and adhered to. Review your risk assessments regularly.
Machinery
A significant part of your risk assessment process will involve the use and maintenance of machinery (generally referred to as ‘work equipment’) which is principally regulated by The Provision and Use of Work Equipment Regulations (PUWER). They require that:
- Work equipment is suitable for the task.
- Is properly maintained.
- That dangerous parts are safeguarded.
- Adequate training and information are provided; and
- Equipment is stable and stop controls, including emergency stops are provided.
*In their guidance document: Farmwife-Your essential guide to health and safety in Agriculture, the HSE highlight that many serious incidents on farms involve machinery, often during maintenance work or unblocking. Some of these incidents have occurred because the machine was unstable; others because guards have been removed. PTO (Power Take-Off) shafts have been involved in many fatal injuries, often when machines are stationary, such as for slurry handling or feed milling and mixing.
Machinery Maintenance
To avoid serious incidents, anyone carrying out maintenance work on farm machinery are advised to use the principals of ‘safe stop’.
What is ‘safe stop’?
‘Safe Stop’ is an ongoing awareness campaign aimed at reducing serious accidents involving farm machinery such as tractors. It’s principals are based upon:
- All movement has stopped before removing any guards.
- Workers are professionally trained to do the job.
- Adequate tools and instructions are provided for maintaining, adjusting, cleaning and unblocking machines.
- Safe working practices are devised and used.
- Stored energy, e.g., from compressed material, springs or hydraulics, is released safely before you start work.
- Hydraulically raised machines or parts are prevented from descending by using mechanical devices such as stops or jacks when people work under them.
Isolating Equipment
There is a large and varied range of work equipment on farms, many generally with dangerous moving parts that can cause serious life changing or fatal injuries. Such Incidents generally occur when maintaining, cleaning or adjusting. Switching a machine off, will not always be enough to prevent an accident, machines that have specific defects are known to come on when in the off position, an even higher risk is when the machine is switched on accidentally or inadvertently.
It is therefore essential that a risk assessment process identifies the need for an isolation and lock-off procedure.
What the Law Says
The PUWER Regulations are quite specific when it comes to dangerous moving parts in machinery. Regulation 11 of PUWER deals with dangerous parts of machinery. It requires employers to take measures to prevent access to dangerous parts of machinery and to stop the movement of any dangerous machinery before a person enters a danger zone.
Consequences of Failure to Act
Failure to adequately manage such activities can have dire consequences. As the following notes describe:
While unblocking a potato harvester, a farm worker stepped down on to the rollers, he was pulled leg first into the machine and became stuck up to his knee. This resulted in burns to the leg, a pulled hamstring, torn calf, broken nerves and hairline fractures to the knee and ankle.
During the resulting HSE investigation, they found that the farmer had failed to implement a ‘safe stop procedure’ to isolate power and stop the movement of the rollers before the worker accessed them.
The Farmer pleaded guilty to breaching Regulation 11 (1) (b) of the Provision and Use of Work Equipment Regulations 1998. He was fined £4,992 and ordered to pay costs of £5,805.
If you have specific questions relating to health and safety in farms and your business, please get in touch with our team of Health and Safety Consultants.