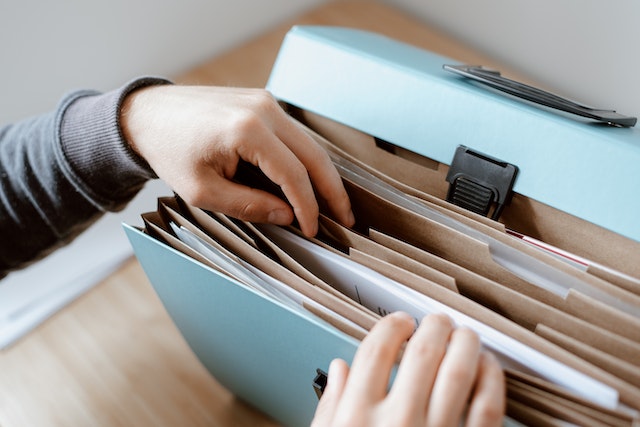
One of the most frequent questions we get asked is: how long I should have to keep records for and what records should be kept? This article aims to provide guidance on record keeping and why businesses need to keep records.
Record Keeping & Safety Management
Record keeping is an important part of your Health and Safety Management System it is your evidence to demonstrate that you are complying with your legal duties under various health and safety legislation.
In order to demonstrate that you meet the requirements for specific regulations you should have documented evidence and different people will want to see your records at different times depending on the document. Enforcement authorities will look for evidence that certification records and internal inspection regimes are in place too, and without this evidence to hand, leads to you being technically in breach of legislative requirements and remember, the HSE can issue you with a Fee for Intervention which is currently at £163 per an hour, so failing to maintain records could be a costly mistake.
The Management of Health and Safety at Work Regulations require that the employer makes a suitable and sufficient risk assessment based upon the risks that the employees are exposed to in connection with their work and also to those who are not in their direct employment who could be affected by the company’s work. If you employ 5 or more people then these risk assessments must be documented, however, if you employ fewer than 5 you do not need to although it is good practice and also demonstrates your commitment to managing health and safety.
PUWER & LOLER Regulations
Other types of records include, servicing and maintenance records, these are important to demonstrate that your equipment provided is safe for use and maintained in a safe condition under the Provision and Use of Work Equipment Regulation (as amended) (PUWER).
Likewise, to comply with the Lifting Operations and Lifting Equipment Regulations (LOLER) the piece of lifting equipment should be subject to a thorough examination and a certificate of this should be held to prove compliance and that the piece of lifting equipment is safe for use. Please be mindful though, a forklift truck which has received a thorough examination may not comply with the PUWER as the whole forklift truck may not have been examined just the components and parts which fall within the requirements of LOLER which include, mast, chains, carriage, forks and tilt mechanism. Whenever receiving any documentation from a third party after carrying out an inspection always check to see what was inspected and assessed.
There are lots of different types of documents that are required to be held and often insurance companies may request to see this information. Furthermore, records retained will also help companies achieve their SSIP accreditations and tender questionnaires.
Reporting of Accidents & Injuries
In order to comply with the Reporting of Injuries, Diseases and Dangerous Occurrences Regulations you must keep a record of any reportable injury, over-seven-day incapacitation, disease or dangerous occurrence. It is a legal requirement to report these as a RIDDOR via the HSE so when you complete the online form you can download the completed record and save a copy.
Furthermore, you must also keep a record where there has been an injury sustained that has risen out of or in connection with the employee’s work which has led them to be incapacitated for three consecutive days and it does not include the day of the accident.
In the event of an accident or incident, an accident/incident investigation should be carried out to establish the cause of the accident/incident. As accidents/incidents are rarely caused by one single factor, it is important as part of the accident/incident investigation to find out the immediate causes and the underlying causes. The information from the accident/incident investigation must be documented and also the findings of the accident/incident should be shared so that lessons can be learnt to prevent it from happening again. By recording your accident/incident investigation and the findings identified, this also shows various interested parties that you have investigated the accident/incident and taken remedial action to prevent re-occurrence.
Health & Safety Records
So far, we have looked at some of the records that should be retained however the following list is a few examples of which health and safety related records should be kept.
- Policy statements and action plans.
- Any risk assessments, their reviews and updates or amendments that you have written for general activities, any risk assessments involving equipment and machinery and any legislation specific risk assessments for example the fire risk assessment, risk assessments for new or expectant mothers, DSE assessments, manual handling, young persons, individual risk assessments, or for chemicals.
- Copies of material safety data sheets.
- Employers’ liability insurance certificates.
- Maintenance, examination, and testing records (including ventilation and extraction equipment, respiratory and other personal protective equipment).
- Environmental monitoring records, for noise, vibration, dust etc or any water and asbestos surveys.
- Medical and Health surveillance records.
- Health and safety training records – especially for inductions, job specific activities and any toolbox talks.
- Minutes of meetings of the Health and Safety Committee (if applicable).
- Safety inspections walk rounds, etc.
- Safe Operating Procedures and Safe Systems of Work.
- Personnel and work records – people, places, tasks.
- Accident book and Reporting of Injuries, Diseases and Dangerous Occurrences Regulations (RIDDOR) reports.
- Accident and incident investigations.
- Annual reports of performance reviews.
- Waste transfer notes.
You have all these health and safety related records but how long do you need to keep them for? Well, a general rule of thumb is five years however there are some exceptions which are:
- Health Surveillance, including medical reports – at least 40 years from the date of the last entry.
- Accident book/record – whichever is the greater: three years from date that the record is created (or last record entered if in an accident book).
- Risks assessments: There is no set amount of time that you need to keep your records relating to general risk assessments. It is good practice, however, to keep them whilst they remain relevant.
- For managing the risks from legionella, the risk assessments, the information on the state of the operation of the system, written control scheme and implementation details should be retained for the time that they remain current and then two years thereafter. Records in relation to the monitoring inspection, tests and checks carried out with the dates should be retained for at least five years.
- Waste transfer notes – Copies to be kept for two years.
- Waste consignment notes – Copies to be kept for three years.
As an example, an employee seriously injuries their hand in an accident on a circular saw bench and requires hospital treatment and many months off work. The Health and Safety Executive may visit site having received the RIDDOR report. They will want to see firstly your accident investigation and report accompanying it. They will need to see the risk assessment covering the use of the circular saw bench and the safe system of work to accompany the risk assessment. They will want to see evidence of service records and proof that the machine has the correct guarding and protection devices in place. You also need to prove the machine has a CE mark or UKCA mark depending on the date of manufacturer/purchase and complies with machinery safety guidance.
Record Keeping & HSE Investigations
The HSE will also ask you to show relevant training records and any evidence of recent update or refresher sessions. They will want to see evidence that checks are being carried out prior to the use of the equipment. Being able to produce these documents, may help prevent prosecution, however, as an accident has occurred, the HSE will look further into their investigation looking at the behavioural issues of the employees and the company. This is where a robust, documented safety management system is most likely to protect you and your business.
After the HSE have gone and the worker returns to work you are likely to receive a solicitor’s letter from the employee informing you of their intention to seek compensation. This is where you must be able to prove that you looked after the equipment and the employee and fulfilled your ‘duty of care’ by completing assessments, undertaking training and proving good supervision. The more information you can produce to help your insurers, the smaller the claim is likely to be. Therefore, in the event of any accident which has resulted in an injury sustained or lost time then all records should be kept for at least three years but ideally five years to allow any time after a claim has been made. An employee has up to three years to bring a claim so if they were to bring a claim at the very end of year three and you decided to discard all your documentation because the three-year window is up it would make it difficult to provide evidence therefore opting for the five years enables that you have that evidence.
To conclude, record keeping is an efficient way demonstrating that your organisation is compliant with current legislation and in the event of a company being prosecuted or sued; it can also be used as part of a legal defence. Poor records mean poor defence, no records mean no defence which in return can be a costly mistake.
For advice and support tailor-made to the needs of your business, get in touch with our team of Health and Safety Consultants today.